Un projet de Stéphane Lavirotte dont les pièces ont été imprimées à SoFAB. Une lampe de plongée est l’équivalent d’une lampe de poche. Généralement peu puissante, elle fournit un faisceau d’éclairage assez resserré (un angle de lumière assez étroit grâce à un déflecteur généralement). Ce type de dispositif est à privilégier pour éclairer des détails à photographier (faune ou flore accrochée).
Fabrication d’une Lampe / d’un Phare de plongée
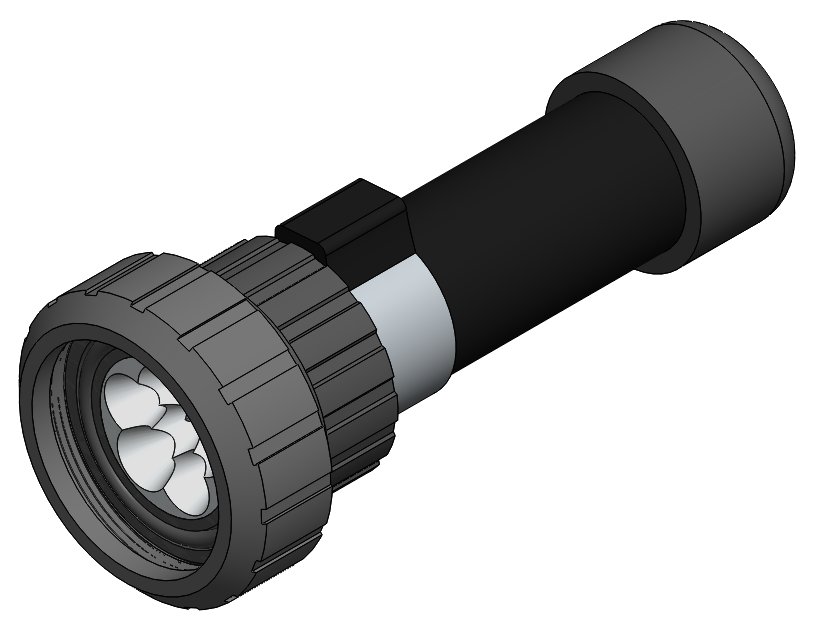
Avertissement: les informations mises à disposition sur ce site le sont uniquement à titre purement informatif et ne sauraient constituer en aucun cas un conseil ou une recommandation de quelque nature que ce soit. En conséquence, l’utilisation des informations et contenus disponibles sur l’ensemble du site, ne sauraient en aucun cas engager la responsabilité de l’auteur, à quelque titre que ce soit. L’utilisateur est seul maître de la bonne utilisation, avec discernement et esprit, des informations mises à sa disposition sur le site.
Attention: A l’heure où vous lisez ces lignes, le projet est quasiment terminé mais n’est pas encore testé. J’ai décidé de créer cette page pour garder une trace des actions réalisées sur cette thématique en attendant la finalisation et l’immersion.
Préambule
Cette page propose la réalisation d’une lampe ou d’un phare avec les mêmes composants de base. Mais commençons par définir ce que nous entendons par lampe et phare.
- Lampe de plongée:
- Une lampe de plongée est l’équivalent d’une lampe de poche. Généralement peu puissante, elle fournit un faisceau d’éclairage assez resserré (un angle de lumière assez étroit grâce à un déflecteur généralement). Ce type de dispositif est à privilégier pour éclairer des détails à photographier (faune ou flore accrochée).
- Phare de plongée:
- Un phare de plongée a une puissance d’éclairage plus importante qu’une lampe et éclaire beaucoup plus largement qu’une lampe (l’angle de lumière est plus important). Ce type de dispositif est généralement utilisé pour filmer sous l’eau et apporter un éclairage plus diffus (ou pour apporter de l’éclairage à une photo d’ambiance à plan large).
Comme nous utiliserons la même source d’éclairage, nous retiendrons dans cette page le critère d’angle d’éclairage pour différencier la lampe et le phare. La lampe sera donc avec l’angle d’éclairage le plus petit et le phare avec celui le plus grand. Nous disposerons donc d’une lampe améliorée car l’éclairage sera aussi puissant que ce que nous utiliserons pour le phare.
Motivations
Si on peut trouver des lampes de plongée à des prix abordables, leur puissance sous l’eau est souvent limitée et donc décevante. Quant au coût d’un phare, il peut s’avérer dissuasif à l’achat. Après une recherche sur Internet sur la fabrication personnelle d’un phare ou d’une lampe de plongée, je suis allé lire le Forum du plongeur qui s’est révélé très instructif sur les expériences de chacun dans la réalisation d’un phare de plongée. En particulier, le projet de phare en PVC a retenu mon attention et semblait très abouti. Ce projet est en fait une succession d’expériences de plusieurs utilisateurs qui ont tous tenté d’améliorer une première version proposée par Yomasterfr.
Ce que je présente ici est donc une reprise des projets proposés par Yomasterfr, Looping33 et Socksou. J’ai décidé de faire une page sur le sujet pour synthétiser ce qui est réparti sur une douzaine de pages sur le forum et surtout donner les plans, la liste complète des composants et où j’ai acheté ceux-ci. Au passage, j’envisage aussi une ou deux améliorations du projet, tout en essayant de faire aussi peu cher. J’espère ainsi faciliter le travail pour d’autres personnes qui se lanceraient dans la construction personnelle de leur lampe ou de leur phare.
Modélisation
Avant de se lancer dans la construction de la lampe ou le phare, il faut avoir une vague idée des plans de construction avant d’acheter les pièces (même si ce n’est pas tout à fait dans cet ordre que j’ai procédé car j’avais l’expérience des projets trouvés sur plongeur.com).
Ce projet a aussi été pour moi l’occasion de découvrir le logiciel de modélisation 3D Solidworks (c) de Dassault Systemes. Pour bien débuter, j’ai consulté quelques tutoriels sur le sujet: pour la prise en main générale, pour les premières étapes de modélisation et pour la modélisation de certaines pièces particulières comme les ressorts. Cela a été assez rapide et m’a permis de modéliser chacune des pièces qui compose la lampe/phare.
L’avantage de cette modélisation est de s’assurer que l’on ne fait pas de défaut de conception et que toutes les pièces vont bien s’emboîter correctement. Cela m’a aussi permis de modéliser la pièce spécifique qui sera produite grâce à une imprimante 3D (nous verrons cela un peu plus tard) et de correctement positionner l’emplacement de l’interrupteur à l’intérieur, et enfin de dimensionner à l’exacte longueur nécessaire le tube en PVC. Bref, de nombreux avantages peuvent être tirés d’une telle modélisation et un rendu sympa avant de pouvoir tenir notre objet.
Voici quelques vues des premières modélisations de la lampe.
Composants nécessaires pour la construction
Je suis reparti des composants utilisés pour la réalisation du projet phare en PVC. Vous trouvez sur cette page la liste détaillée des pièces à se procurer, les liens sur les différents sites où les pièces détachées ont été commandées et un résumé des coûts au moment de l’achat (2014-2015).
Le projet se décompose en deux parties principales: le système d’éclairage et l’enveloppe étanche pour embarquer celui-ci. Commençons pas l’enveloppe qui devra être étanche et résister aux pressions rencontrées en plongées (soir 5 bars à 40 mètres ou 7 barres à 60m). Pour le moment, n’étant que niveau 2, je ne peux descendre que jusqu’à 40m accompagné par un moniteur. Donc une étanchéité à une pression de 5 bars est suffisante. Pour assurer une bonne résistance, je suis parti sur des pièces en PVC qui résistes à une pression interne de 16 bars (soit plus du double de la pression de 7 bars à 60m). On dispose donc d’une marge de sécurité.
Pour réaliser la lampe et le phare, j’ai réfléchi à deux modèles pour l’enveloppe étanche. Un modèle à tête large qui peut accepter la tête de LEDs avec son réflecteur (donc une lampe dont le faisceau lumineux sera plus concentré) et un modèle plus compact avec la tête de LEDs sans le réflecteur (donc à éclairage plus large, soit un phare). Ce qui est un peu surprenant par rapport aux modèles du commerce est que la lampe sera moins compacte que le phare au niveau de la tête car il faut la place pour loger le réflecteur qui a un diamètre plus important que la tête de LEDs.
Lampe de plongée
Voici le plan de construction de l’assemblage des éléments pour réaliser la lampe. Il est toujours plus facile de réaliser ce que cela va donner avec un petit schéma (j’ai fait ce premier schéma avant la modélisation 3D décrite ci-dessus). Ci-dessous, vous trouverez la liste des pièces correspondant à la construction de la lampe:
Lampe étanche en PVC Pression (16 bars) avec tête large de 63mm:
- Raccord Union 3 pièces à coller 63mm
- Réduction incorporée 63/50mm
- Tube de diamètre 50mm
- Bouche femelle à coller 50mm
- Colle PVC pression rigide
Phare de plongée
Voici le plan de construction de l’assemblage des éléments pour réaliser la phare. Il est toujours plus facile de réaliser ce que cela va donner avec un petit schéma. Vous trouverez ci-dessous la liste des pièces correspondant à la construction du phare.
Phare étanche en PVC Pression (16 bars) avec tête compacte de 50mm:
- Raccord Union 3 pièces à coller 50mm
- Tube de diamètre 50mm
- Bouche femelle à coller 50mm
- Colle PVC pression rigide
Partie électrique commune à la lampe et au phare
- LED 1200 lumens – 6 Cree Q5 WB
- Accumulateurs et Chargeur – 2 x 18650, 3.7v 2600mAh
- Relais Reed (interrupteur à lame souple + aimant d’un système de détection d’ouverture de porte)
L’élément important est de pouvoir disposer d’une enveloppe d’objet sans créer de fragilité, donc sans percer la structure (bouton poussoir par exemple) car l’étanchéité est très difficile à réaliser surtout avec la mise en pression. Pour résoudre ce problème, il est possible d’avoir recours à un interrupteur à lame souple (ILS ou Interrupteur Reed). La plupart de ces interrupteurs sont vendus sous la forme d’une ampoule de verre contenant la lame souple. Mais ce type d’interrupteur risque d’être trop fragile pour une utilisation du phare (risque de casser l’ampoule lors de la recharge des accumulateurs). C’est ce même type d’interrupteur qui est utilisé dans un système de détection d’ouverture de fenêtre avec l’avantage dans ce cas que l’ILS est dans une coque plastique, donc beaucoup moins fragile. J’ai opté pour cette solution. Je disposais déjà de l’interrupteur par contact magnétique, donc je ne l’ai pas acheté, mais j’ai mis un exemple de produit si vous souhaitez en commander un.
Pour les accumulateurs, j’ai pris des UltraFire BRC 18650 3000mAh 3.7V Li-Ion, mais j’ai pu voir ultérieurement, que ce sont en fait de faux produits (des produits chinois à pas cher quoi). Il ne faut pas prendre ce modèle si vous souhaitez vraiment avoir l’autonomie indiquée de 3000mAh. En fait, ils ne font que 800 à 900mAh. D’un autre côté, vu le prix (3,63 € sans le port), il ne fallait pas s’attendre à beaucoup mieux mais cela m’a permis de tester pour une somme très modique). Attention ces batteries 18650 Li-Ion peuvent présenter des dangers en cas de mauvaise utilisation et de court-circuit.
Voici donc pour la partie électrique du projet. Rien de bien sorcier. Passons à la réalisation, maintenant que nous disposons d’un modèle à réaliser et des pièces pour construire le tout.
Instructions pour la réalisation
Voici les étapes que j’ai suivi pour la réalisation du phare de plongée.
Phare: démontage du réflecteur de lampe
La tête de LEDs est fournie avec un réflecteur permettant de concentrer le faisceau lumineux de la lampe avec un angle assez étroit (une vingtaine de degrés). Il est assez facile de démonter ce réflecteur de la tête de LED pour augmenter l’angle d’éclairage. Le réflecteur est vissé au culot de la tête de LEDs par l’intérieur. Pour le démonter, il faut tout d’abord désolidariser le culot de la tête de LED. C’est enfoncé à force.
Il suffit de s’équiper d’un petit tournevis plat, fin et d’un marteau. Placer le tournevis à la limite entre la partie en laiton et la partie en aluminium du culot de la tête LED. Donner un petit coup de marteau sur le tournevis. Ceci va avoir pour conséquence d’écarter les deux parties. Il vous suffit alors de faire levier avec le tournevis tout en tournant le culot pour faire augmenter régulièrement l’espacement entre la partie de laiton et la partie en aluminium. Le culot en laiton sort alors de son logement.
Utiliser un tournevis cruciforme pour enlever les deux vis à l’intérieur. Il suffit alors de tirer manuellement sur le déflecteur pour l’enlever. Si vous souhaitez remonter ce déflecteur, pensez à faire une marque sur le déflecteur et le culot en aluminium pour pouvoir réaligner correctement les deux parties (le déflecteur peut se ré-emboiter facilement). Ceci vous permettra ainsi de revenir au montage de départ, même si on ne revisse pas le tout.
Fabrication du verre en poly(méthacrylate de méthyle)
Le poly(méthacrylate de méthyle) ou PMMA est plus connu sous son premier nom commercial de Plexiglas ou maintenant Altuglas. Ce plexiglas peut être de deux types: extrudé ou coulé. Il est préférable de prendre du plexiglas coulé plutôt qu’extrudé (le résultat à la découpe est plus net, ce qui est important dans notre cas).
Pour déterminer la dimension de découpe de notre verre en Plexiglas, j’ai démonté le raccord union 3 pièces femelle. Il faut alors mesurer les dimensions de la pièce sans filetage pour déterminer le diamètre. Le diamètre de notre verre doit être de:
- Pour le raccord union 63mm (lampe): 78.5mm de diamètre
- Pour le raccord union 50mm (phare): 62.85mm de diamètre
L’épaisseur du verre est un paramètre importante car c’est une surface plane sur laquelle la pression de l’eau peu facilement engendrer une déformation (plus facilement que sur un cylindre). Étant donné le diamètre, j’ai choisi une épaisseur de plexiglas de 8mm. Pour avoir une découpe propre des bords, j’ai eu recours à la découpe laser disponible au FabLab de Sophia Antipolis; le SoFab dispose d’une Trotec Speedy 100. Il suffit alors de récupérer un des fichiers ci-dessus pour réaliser la pièce. Le Plexiglas est de l’Altuglas que j’ai trouvé pour un prix très modique chez Balitrand. Ils vendent des chutes de plexiglas pour environ 5 euros (quelle que soit la taille de la chute). J’ai ainsi pu acquérir une grande plaque pour 5 euros permettant d’un réaliser une bonne trentaine de verres… Largement suffisant pour mon projet.
Fabrication du coupleur d’accumulateurs
Le montage électrique est des plus simpliste d’un point de vue connectique. Par contre, faire un système qui soit pratique à manipuler pour sortir les batteries et qui permette de fixer celles-ci dans le manche pour éviter que cela ne bouge dans tous les sens est un peu plus délicat. J’ai donc réalisé la modélisation de cette pièce à l’aide Solidworks qui a été d’un grand secours et m’a permis la conception d’un support pour les accumulateurs et d’y incorporer l’interrupteur ILS (la partie interne).
Une fois cette modélisation réalisée, il ne reste plus qu’à lancer l’impression du modèle 3D obtenu. Retour au SoFab (le Fab Lab de Sophia Antipolis) et cette fois-ci on utilise la Creatr’ de Leapfrog pour produire notre pièce. Vous trouverez le paramétrage utilisé lors de l’impression sur la capture d’écran ci-dessus. Le logiciel utilisé est Cura. 2h27 plus tard, on dispose de notre coupleur d’accumulateurs adapté à notre projet. Bon je passe sur la petite erreur de modélisation qui portait sur une erreur de la taille du logement pour les piles. Et oui, 0.1mm de marge pour faire glisser les piles, c’est vraiment trop juste, surtout quand on voulait mettre 1mm…
Après une tentative infructueuse de retravailler la pièce, je suis rapidement venu à la conclusion qu’il fallait corriger le modèle et le réimprimer. Bref, une deuxième impression plus tard, tout va mieux. Pour la deuxième impression, la vitesse d’impression a été modifiée pour avoir la version 2 plus rapidement (on passe de 40mm/s à 60mm/s). Avec la modification du modèle, nous sommes arrivés à 1h59 d’impression (donc avec un coût de fabrication de la pièce légèrement inférieur, 5€ de moins environ).
Pour ceux qui seraient intéressés de reproduire exactement ce projet, voici le fichier (corrigé) d’impression de la pièce au format STL.
Assemblage du coupleur de piles
Le premier élément à assembler est le coupleur de piles. Pour réaliser celui-ci, nous avons besoin des éléments suivants:
- La pièce que nous venons d’imprimer
- Un ressort au fond du tube (récupéré sur un coupleur de piles AA)
- Deux petits morceaux de gaine thermo-rétractable
- Un morceau de fil électrique de 2,5mm²
- Un interrupteur ILS
Il faut tout d’abord passer un des fils électriques de l’interrupteur ILS dans le petit trou prévu à l’extrémité du coupleur de piles et venir y souder le ressort. Dans mon cas particulier, le ressort disposait déjà d’une attache et d’un petit fil, mais celui-ci sortait perpendiculairement par rapport au ressort. J’ai donc collé le ressort à un petit morceau de plastique de 2mm d’épaisseur et qui faisait environ le diamètre du logement de piles.
Il faut ensuite souder le ressort (où le fil associé au ressort) au fil de l’ILS que nous avons donc préalablement passé par le trou de l’extrémité du coupleur. Une fois la soudure des deux fils effectuée et la gaine thermo-rétractable mise en place, il suffit alors de tirer doucement sur le fil pour faire entrer le ressort (et son support éventuel) au fond du logement de piles.
Pour réaliser le contacteur sur la partie supérieure du coupleur, utiliser un fil électrique en cuivre de 2,5mm². Enlever sa gaine plastique protectrice. Utiliser la goulotte pour cintrer le fil avec le bon rayon. J’ai légèrement martelé le fil pour que celui-ci soit plat sur la surface supérieure et ainsi faciliter le contact avec le ressort de la LED (pour éviter le glissement). J’ai ensuite réalisé un petit trou de 1mm de diamètre avec une perceuse à colonne dans le fil de cuivre pour passer le deuxième fil de l’interrupteur ILS et les solidariser par une soudure. Enfin, un petit morceau de gaine thermo-rétractable vient protéger le tout.
Pour terminer le montage, j’ai utilisé un pistolet à colle pour coller l’ILS dans le logement prévu à cet effet, ainsi que le l’anneau en cuivre dans la partie supérieure du coupleur. Nous arrivons ainsi au montage suivant pour le coupleur de piles.
Assemblage de l’enveloppe PVC
Avant d’assembler l’enveloppe en PVC dans laquelle nous glisserons le coupleur de piles, les piles et la tête de LED, il nous reste à résoudre un dernier problème: calculer la longueur optimale pour le tube en PVC. Pour calculer cette longueur, il faut bien entendu à minima que ceci permette d’insérer le coupleur de piles. Mais grâce à l’utilisation de Solidworks, il est aussi possible de calculer le centre de gravité de l’objet. Cela permettra ainsi de vérifier l’équilibre de la lampe lors de la prise en main.
Calcul du centre de gravité ou d’inertie de l’objet
Petit rappel: le centre de gravité est le point d’application de la résultante des forces de pesanteur. Le centre d’inertie ou centre de masse est le barycentre des masses et le point de l’espace où s’appliquent les effets d’inertie c’est à dire le vecteur variation de quantité de mouvement. En des termes plus simples, si l’on veut faire tourner un objet, c’est en mettant l’axe de rotation au centre d’inertie que l’on fournit le moins d’effort. Dans le cas où l’on peut considérer le champ de gravité comme uniforme, le centre d’inertie est confondu avec le centre de gravité. Dans notre cas, on pourra donc parler sans distinction du centre de gravité ou du centre d’inertie, le champ de gravité sur notre lampe étant uniforme.
Pour réaliser cette étape, j’ai associé dans Solidworks à chacune des pièces de la modélisation la matière avec laquelle celle-ci est réalisée. Cela permet au logiciel de faire un calcul de la masse de chaque pièce. J’ai vérifié celui-ci à l’aide d’une balance électronique (au gramme près) et corrigé les estimations lorsque cela était nécessaire (par exemple pour la tête de LEDs qui est creuse mais que je n’ai pas modélisé comme tel).
Solidworks permet non seulement d’estimer la masse, le centre de gravité mais aussi le volume d’un assemblage de pièces. Vous pouvez voir sur la photo ci-dessus les propriétés pour le montage global. Le logiciel permet alors de représenter la position du centre de gravité sur la modélisation. Il faut pour cela ajouter le centre de masse (que l’on trouve dans Géométrie de Référence) puis éditer un composant de l’assemblage pour que l’objet s’affiche en filaire et placer le curseur sur la propriété centre de masse.
Comme on pouvait s’y attendre, on voit sur le schéma ci-dessus que le centre de gravité n’est pas au milieu de la partie visible du tube par lequel nous tiendrons la lampe. Il y a donc un déséquilibre potentiellement à corriger. Mais l’utilisation de cette lampe ne se fera pas sur terre, mais dans l’eau. Or le volume de la partie avant de la lampe est plus important que le volume de la partie arrière. Donc la poussée d’Archimède aura tendance à plus faire flotter la partie avant que la partie arrière de l’objet. Il est donc maintenant temps de calculer les volumes et de déduire la poussée qui en résulte. On pourra ainsi en déduire non seulement l’équilibre en main (la position du centre de gravité), sur terre comme sous l’eau, mais aussi s’il est nécessaire de lester la lampe.
Calcul de la flottabilité
Le calcul du volume par Solidworks fonctionne à partir du calcul de matière sur des volumes pleins (il ne semble pas possible de calculer simplement le volume de l’enveloppe externe). Pour réaliser ce calcul, j’ai donc dû modifier la modélisation pour remplir toutes les parties vides (dans le tube et la tête de LEDs).
A l’aide des propriétés de la modélisation modifiée, on peut calculer un volume pour la lampe est d’environ 700cm3 donc 0,7dm3 (699.636mm3 pour être précis). La masse volumique de l’eau salée est d’environ 1030kg/m3 donc 1,03kg/dm3 (ou litre). Il est possible de calculer plus précisément la masse volumique de l’eau de mer, en fonction des propriétés de salinité, de température et de pression. Pour la mer méditerranée avec une salinité de 37g/L, une température moyenne de 18°C (24 en surface et 13 au fond), et une pression absolue de 5 bars à 40m, on trouve une masse volumique de 1027,75kg/m3.
Le poids de l’eau déplacée par le lampe est donc de: 0,7*1,028 = 0,7196kg donc environ 720g d’eau salée (où environ 700g d’eau douce, la masse volumique de l’eau douce étant 1kg/l). Avec un poids estimé de 750g, la lampe doit donc avoir un poids apparent nul donc une flottabilité nulle soit l’équilibre. Donc nul besoin de la lester sauf à rééquilibrer le poids entre l’avant et l’arrière et donc déplacer le centre de gravité. Toutefois, il faut tenir compte de la poussée d’Archimède suivant les différentes parties de la lampe. En effet, la tête étant plus volumineuse, elle subira une poussée plus forte que l’arrière, mais elle est aussi plus lourde. Nous allons donc calculer le volume de la tête et celui de l’arrière, le tube en lui même étant d’un volume constant sur toute sa longueur.
Le volume de la tête de lampe est de 354cm3 alors que l’arrière n’est que de 126cm3 ce qui fait un rapport de 1/3 environ. Donc la poussée d’Archimède devrait être 3 fois plus forte sur l’avant de la lampe que sur l’arrière. Il faudrait donc que le centre de gravité soit au 1/3 de la distance du tube apparent (qui lui reçoit une poussée uniforme) par lequel nous allons tenir la lampe. On peut doc voir sur le schéma précédent que celui-ci est bien un peu trop vers l’avant de l’objet. Si on veut légèrement le faire reculer, il est nécessaire d’ajouter un poids sur l’arrière, donc vers le bouchon arrière du tube. Pour calibrer le poids nécessaire, une fois de plus Solidworks a été très utile, même si j’ai du procéder par test. J’ai donc rallongé le tube pour pouvoir y glisser le leste et prévu un leste de 42mm de diamètre. La masse volumique de référence que j’ai utilisée est de 7300kg/m3 correspondant à un morceau de fonte ou bien encore à la masse volumique de la grenaille de plomb. Avec ces propriétés, il faut un morceau d’une hauteur de 15mm pour déplacer le centre de gravité au 1/3, ce qui fait une pièce d’environ 150g donnant ainsi une flottabilité légèrement négative à l’ensemble.
Il est donc nécessaire d’allonger le tube de 15mm, sa longueur minimale pour contenir le coupleur de pile étant de 175mm. Donc en coupant le tube à une longueur de 190mmm et en ajoutant le leste prévu ci-dessus, nous devrions disposer d’un phare correctement équilibré en main sous l’eau et avec une flottabilité légèrement négative.
Bague avec l’aimant interrupteur
Il reste à finaliser une bague sur laquelle l’aimant interrupteur sera fixé. Pour le moment le bouchon à l’arrière de la lampe n’est pas collé pour pouvoir passer cette bague qui permettra de faire coulisser l’aimant en face de l’interrupteur ILS à l’interieur pour démarrer l’allumage de la lampe.
Assemblage final
Il ne reste maintenant plus qu’à découper le tube à la longueur de 190mm puis assembler et coller les différentes pièces entre elles. Pour réaliser la découpe du tube, j’ai utilisé une scie sauteuse avec une lame longue permettant de découper proprement un diamètre de 50mm.
Le collage est une étape importante. En effet, c’est la qualité du collage qui permettra d’assurer l’étanchéité de notre objet. J’ai donc utilisé les composant suivants:
- Papier de verre avec une taille de grain fin
- Décapant PVC
- Colle PVC gel pour PVC pression
Pour réaliser le collage, commencer par poncer à l’aide du papier de verre les parties à assembler. Puis nettoyer à l’aide du décapant et d’un chiffon propre le raccord et le tube à assembler. Enfin appliquer une mince couche de colle sur les 2 parties à assembler dans le sens longitudinal puis emboiter immédiatement sans tourner. Essuyer les bavures à l’aide d’un chiffon sec et ne pas manipuler l’assemblage pendant 5 minutes. Une fois l’ensemble des collages réalisés, il faudra attendre 24h avant de pouvoir se lancer dans les tests grandeur nature.
Voici quelques photos pour montrer l’assemblage final de l’objet réalisé.
Utilisation et tests de mise sous pression en situation
Mais le plus dur reste à faire: réaliser des tests de résistance à la pression en plongée… Il ne reste plus qu’à attendre la prochaine plongée et à croiser les doigts car je n’ai pas encore réalisé cette ultime opération primordiale. Je pense déjà faire descendre le corps de la lampe (légèrement lesté) lors d’une première plongée et vérifié que tout est bien étanche. Puis de faire une descente avec la partie électrique. Mais est-ce que cela fonctionnera vraiment ? Sinon, cela me fera une super lampe torche pour le garage… ;(
Coût total de la lampe
Pour résumer, le coût d’un tel projet est:
Enveloppe PVC Pression | |
Union trois pièces 63 mm à coller PVC pression | 7.15€ |
Tube diamètre 50 mm PVC pression 1,15 mètre> | 13,20€ |
Réduction incorporée 63/50 mm PVC pression> | 1,40€ |
Bouchon femelle à coller 50 mm PVC Pression | 2,19€ |
Frais de port | 6,38€ |
Total enveloppe PVC | 30,32€ |
Partie électrique | |
LED 1200 lumens – 6 Cree Q5 WB | 20,20€ (port inclus) |
Accumulateurs et Chargeur – 2 x 18650, 3.7v « 3000 » mAh | 8.13€ (port inclus) |
Interrupteur Reed (ILS) | 4€ |
Total matériel électrique | 28,33€ |
Fabrication FabLab | |
Découpe laser | 0,41€ (1 minute de découpe à 25€/h) |
Impression 3D | 24,50€ (2h27 à 10€/h) |
Total fabrication | 24,91€ |
Coût total | 83,56€ |
A noter que le tube PVC d’1,15m permet de réaliser plusieurs pièces. Donc, dans le cas du deuxième équipement construit sur la même base, le coût pour le phare sera de 13,10€ de moins (pas de coût de tube, mais le raccord union est 0,10€ plus cher) soit environ 72€ si vous rachetez des accumulateurs ou 70€ si vous utilisez les mêmes pour les deux (et donc que vous ne partez pas en plongée avec les deux en même temps). Bref, cela vous fait une moyenne de 75€ le projet, soit 2 fois moins cher pour une lampe « équivalente » et beaucoup, beaucoup, beaucoup moins cher qu’un phare.
Remerciements
Je tiens à remercier ici quelques personnes qui ont contribué à faire concrètement avancer ce projet:
- mon fils Gaëtan avec qui nous avons découvert Solidworks et qui m’a aidé à modéliser une partie des pièces de la lampe
- les différentes contributeurs du forum de plongeur.com et en particulier Yomasterfr, Looping33 et Socksou pour leurs réalisations qui m’ont donné le goût de m’y mettre aussi
- mes parents pour le prêt de leur balance de pâtisserie pour vérifier précisément le poids des différents pièces
- mes collègues Jean-Yves, Gaëtan, Denis, Claudine et Paul avec qui j’ai pu discuter de ce projet lors de pauses café
- le Fab Manager de SoFab, Marc, pour la formation sur les différentes machines utilisées et les bonnes idées d’évolutions du projet actuel